SHIRT FINISHERS
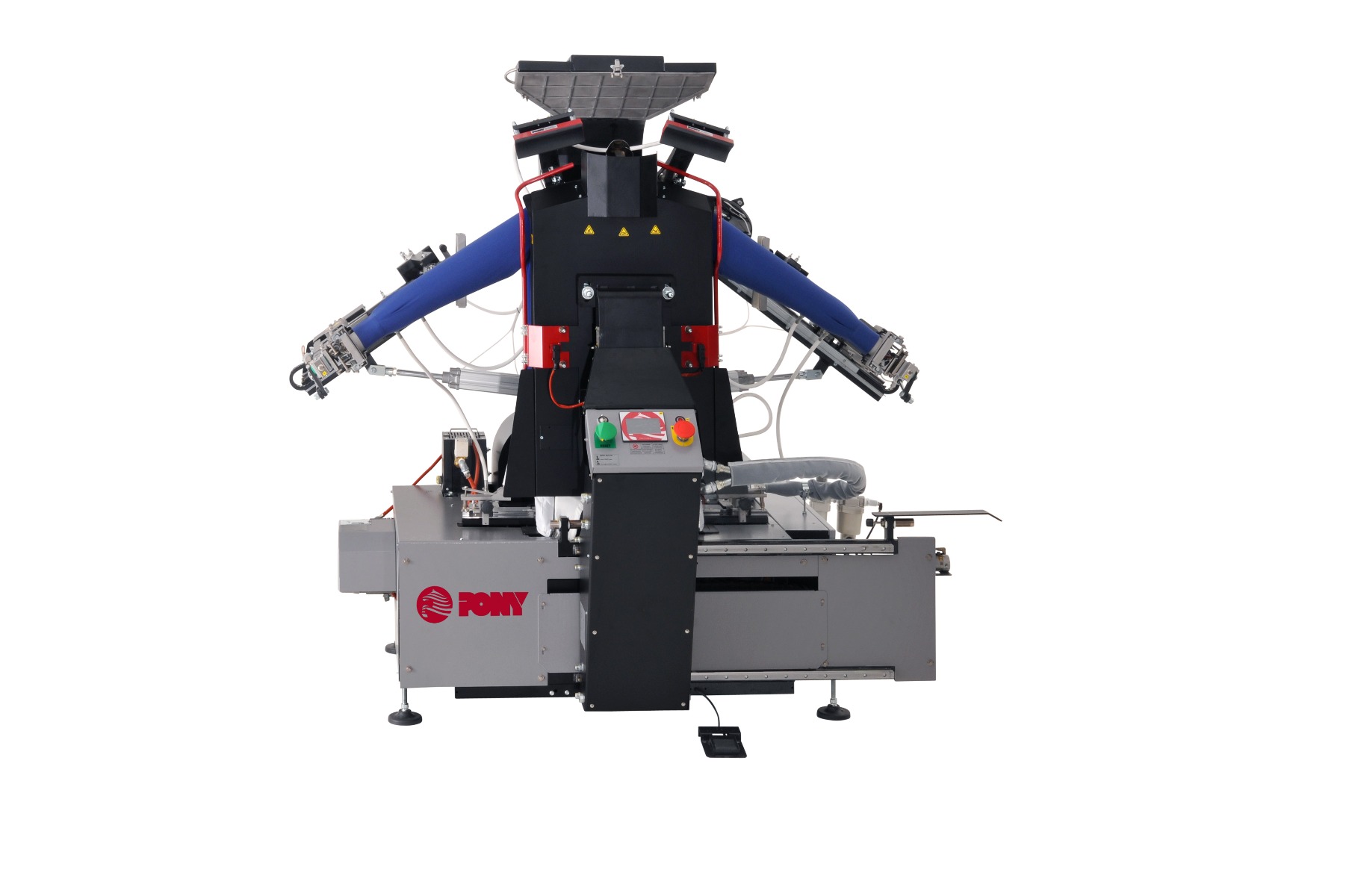
One of the many innovations we presented at the EXPO-DETERGO 2018 was our new version of single-buck shirt press ANGEL This machine, the only one in its range that can claim to be 100% made-in-Italy, allows an impressive hourly production of around 60 pieces, for shirts that are washed and tumble-dried at about 1,200 rpm.
This shirt press combines highly professional performance with extreme ease of use. Thanks to its simple, intuitive controls it can be used even by unskillful operators, with reduced labor costs, while the fine tolerances used in construction and the high quality finish avoid any final shirt touching-up: energy consumption is vastly reduced and the finishing quality is always to the same uncompromising high standard and consistent in finish.
The high standard finish makes its performance of great interest even for Italian and European markets (usually known for their high requirements from this side), in addition to the American market of course.
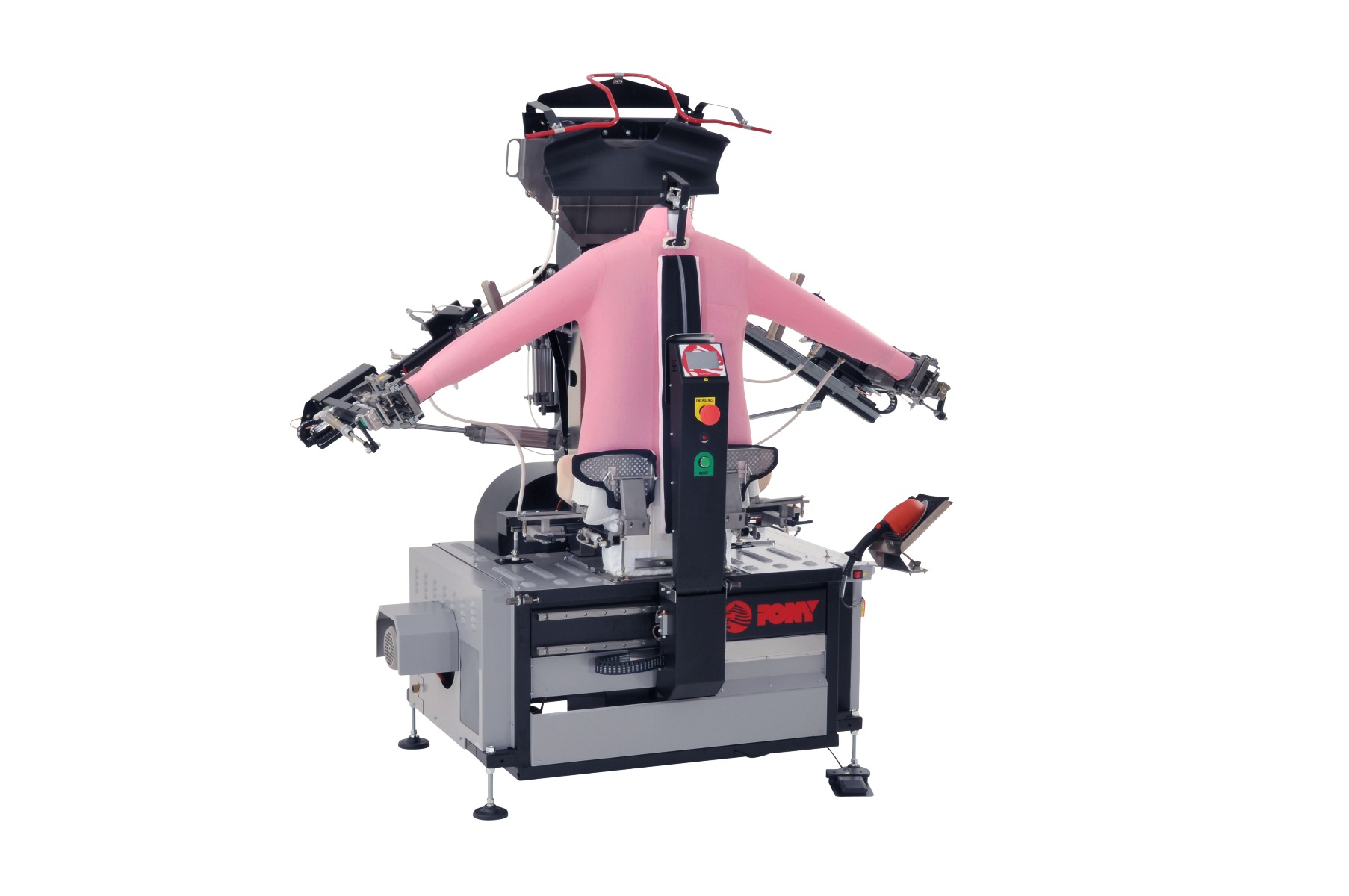
Still at expodetergo 2018 PONY introduced its latest version of he EAGLE 2.0.This shirt finisher has a wide range including men’s shirts, women’s blouses, polo shirts, medical uniforms, and chef’s uniforms. This machine drew on our many years of manufacturing experience and customer interaction to meet the ultimate goal of reducing energy consumption and machine size. It makes a state of the art shirt finisher affordable for every shirt laundry.
The H.A.R.S. (Hot Air Recovery System), is an efficient system for the recapture of air from the shoulder press. This device maintains a constant 150° air temperature and conveys the air through a special channel into the fan to speed the drying of the shirt, reducing energy consumption by 20 to 30%, with faster drying times and higher productivity. It is the only shirt finisher in the world pressing both the yoke and the tucks at the same time, with Teflon press heads to avoid marks on dark fabrics.
Additional innovations include the front horizontal sliding paddle and a brand new adjustable cuff clamps system, with rotating rounded clamps. The PLC TOUCH SCREEN managing functions and finishing cycles, is adjustable and integrated in the main frame. For the operator's convenience, the controls of the basic functions are repeated on the front paddle with customizable buttons. If connected through an Ethernet port, it is possible to control the Pony Touch Technology even from remote locations.
The "TOTAL ELECTRIC" shirt finisher version, in conjunction with the "totally electric" version of the collar and cuff press, allows the installation of a highly productive and professional shirt ironing system anywhere without the requirement for steam or water. The "TOTAL ELECTRIC" version also offers the opportunity to select the "ECO" or "PRO" operation according to different electrical powers available and production volumes.
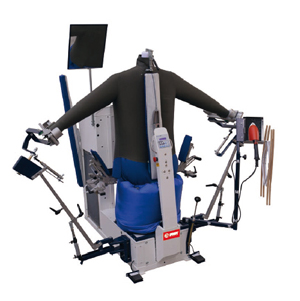
Model 404, thanks to its upgraded technical features, grants a high finishing quality on shirts, lab-coats and uniforms, washed and tumble-dried, which need only little steam and overheating to dry quickly, and pneumatic tensioning to stretch the seams. This machine is equipped with a front paddle with pneumatic closing device, and a vacuum steam-heated counter paddle. Both paddles are padded to avoid the marks of buttons or to prevent the pressure from leaving marks or a polish effect on the fabrics, especially on dark ones.
The hem is blocked by a rear clamp and two side clamps, and is tensioned by a pneumatic trolley. The sleeve clamps are air-operated and their height is adjustable. Operational cycles are managed through a microprocessor with either 10 saveable programmes or manual cycles.
With a simple flick of a switch this finisher is set into “coats” mode (jackets, coats, hotel uniforms, dresses etc., all garments that need a large quantity of steam and a lower drying temperature). In this case the sleeve clamps and the side/rear clamps are excluded.
Model 403 is slightly different, having less automation. Operations are mainly manual. Its reduced price makes it more affordable even for medium- or small-sized businesses where the advantages of a professional form finisher are anyway essential.
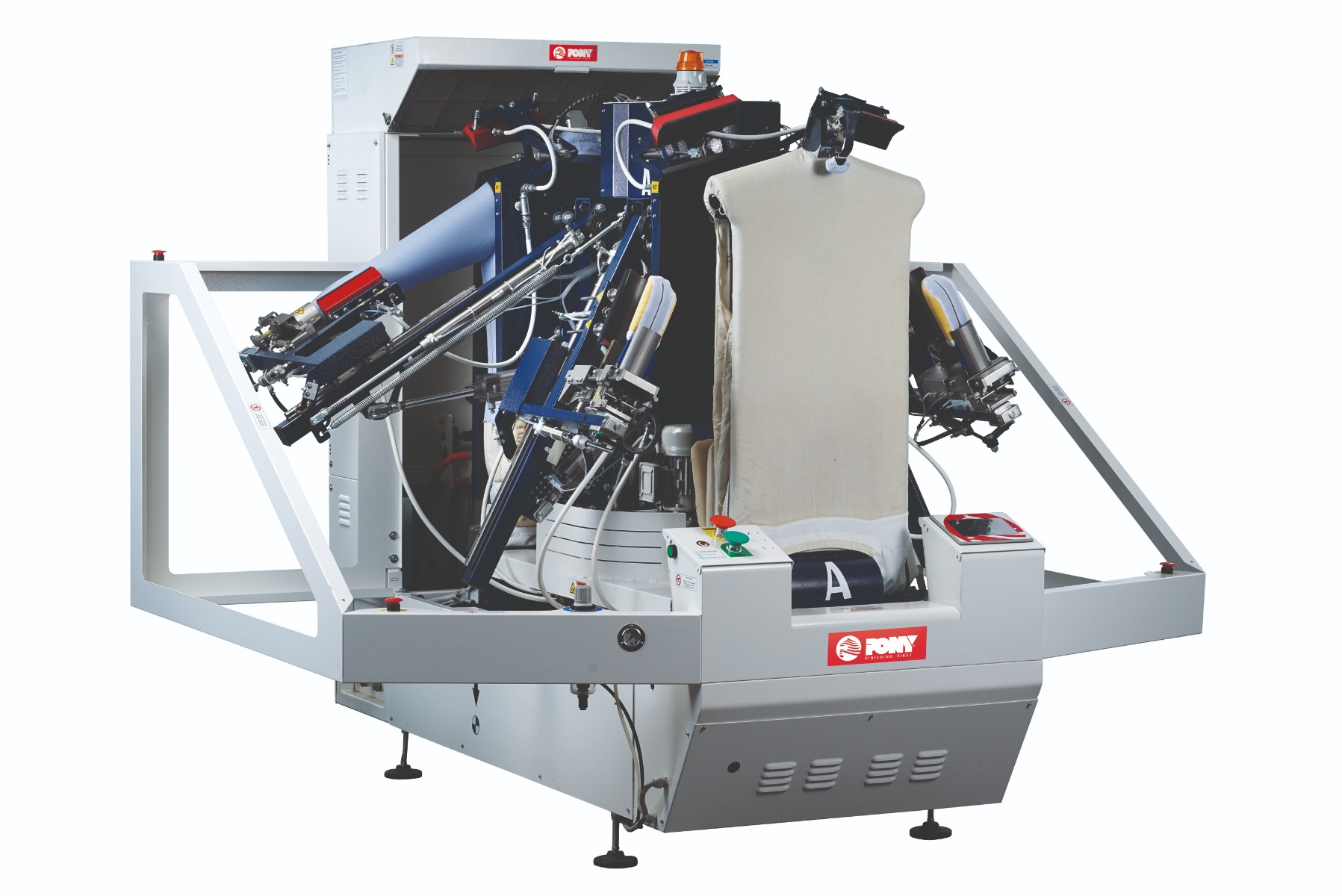
And last , but not the least, our double-body rotary shirt press Model DB360.
The DB360 is conceived and designed to obtain maximum productivity, with incomparable finishing quality and no increase in costs.
Features:
- Compact rotary structure, with finisher rotary system and both start and braking system electronically controlled with energy recovery.
- Vacuum group, integrated in the rotating part.
- New steam circuit integrated in the machine to reduce heat dispersions and condensations.
- Integrated shoulder-press in action during rotation.
- Three pressing cycles: short , long, special with the exclusion of the rear buck
- Integrated Safety devices in the lateral protection bars limiting the work area, with sound and light signal when machine in action.
- Height adjustment and ergonomic work station.
- New full-color touch PLC, simple and intuitive, managing cycles, diagnostics, emergency and pre-set maintenance.
- Energy Saving pneumatic system.
- Compact size to ease transportation and installation.
- Adaptable structure for transit through standard doors (90 cm).
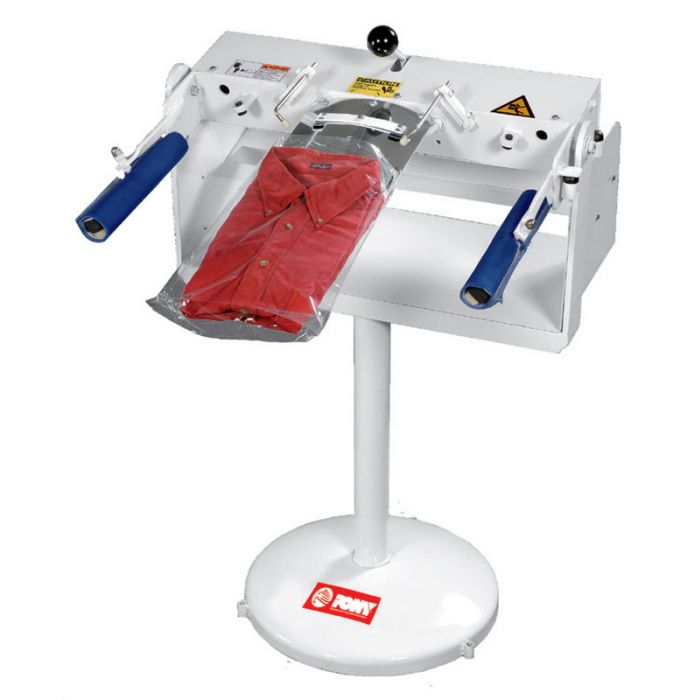
PONY produce a shirtfolder that allows to handle also this phase of the process properly.
The PCM shirtfolder, manually operated, is very easy to use and requires no installation and very little maintenance. The operational sequence consists of a few rapid moves, after which your shirt will come out folded, bagged and ready for delivery.